The production of a forged flange is a meticulous process that involves several stages. It starts with the selection of the right material and ends with packaging for delivery. In this blog post, we will take a deep dive into each step of the forged flange production process.
Step 1: Material Selection
The first step in the production of a forged flange is the selection of the right material. The material used can vary depending on the application of the flange. Commonly used materials include carbon steel, stainless steel, alloy steel, and more. This step is crucial as it directly impacts the durability, strength, and corrosion resistance of the final product.
A105N material, for example, is commonly used for forged flanges in high-pressure and high-temperature applications.
Once the material is selected, it undergoes a heating process to make it malleable. The temperature at which the material is heated depends on its composition and desired properties. Typically, the temperature ranges from 2000 °F to 2400 °F.
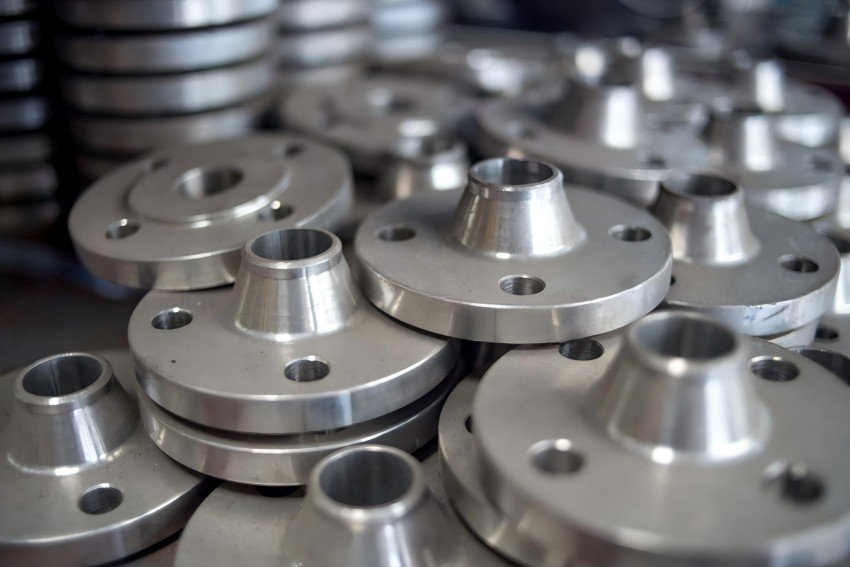
Step 2: Forging
After the material is heated, it is ready for forging. This process involves shaping the heated material into a desired flange shape using extreme pressure and force. The forging process can be done with different techniques such as drop-forging, press forging, or ring rolling. Each technique has its benefits and is chosen based on the size and complexity.
Drop-Forging
Drop-Forging is a forging process where a hammer is raised and then “dropped” onto the workpiece to deform it according to the shape of the die. The main types of drop forging are open-die drop forging and closed-die drop forging. This method is widely used because of its ability to refine the grain structure and improve physical properties of the metal.
Drop forging is typically used for the production of slip-on flanges and socket weld flanges. These types of flanges benefit from the refining of the grain structure and the improved physical properties that the drop-forging process provides. This process ensures these flanges can withstand the high pressure and temperature conditions they are often subjected to.
Press Forging
Press Forging, unlike drop forging, applies a slow, continuous pressure to shape the metal. The pressure is applied using a hydraulic press. This method minimizes the cooling of the workpiece during forging and allows for a high degree of shape complexity and a better surface finish compared to other methods.
Press forging, on the other hand, is often used in the production of complex flanges such as weld neck flanges and threaded flanges. These flanges have intricate designs that require a higher degree of shape complexity, which press forging can achieve. The better surface finish provided by press forging is also beneficial for these flanges, as it enhances their sealing ability, reducing the risk of leakage.
Ring Rolling
Ring Rolling is a specialized type of hot rolling that increases the diameter of a ring by reducing its thickness. The rolling process can be achieved with an open-ended set of flat or shaped rolls. It’s commonly used to create components that are stronger and lighter than those made through traditional forging methods. This process is particularly useful in the production of large-scale, high-quality circular components.
Ring rolling is primarily used for the production of large-scale, high-quality circular components like large diameter flanges. Large diameter flanges are commonly used in heavy equipment and industrial pipe systems where high strength and lightweight components are necessary. The ring rolling process ensures these flanges have improved strength and are lighter than those made through traditional forging methods.
Step 3: Machining
Once the forging process is completed, the next step is machining the forged flange. This is where the flange is further refined and shaped into the exact dimensions specified by the customer.
In the industry, a variety of machining techniques are employed depending on the intricacy of the design, the level of precision needed, and the specific material of the flange.
One of the most common machining techniques is turning, where a lathe is used to shape a spinning work piece with a cutting tool. This process is particularly effective for creating cylindrical parts and is typically used for shaping the outer and inner diameters of the flange.
Another common method is drilling, which is used to create holes in the flange. This is crucial in flange production as it allows for the secure attachment of the flange to a pipe or another flange.
Milling is another technique used, where a rotating cutting tool is moved across the work piece to remove material. This method is typically used to create more intricate shapes or features on the flange, such as grooves or slots.
The machining process often involves several passes of these techniques to achieve the desired dimensions, and it is critical in ensuring the flange fits correctly in its intended application. Care and precision in this step are vital for the overall quality and functionality of the final product.
Step 4: Inspection
After forging and machining, the product is inspected to ensure that it meets the necessary specifications. This inspection process includes visual inspection, dimensional checks, and sometimes additional non-destructive tests. Any flanges that do not pass the inspection are either corrected or discarded.
The flanges that do not pass the inspection will be assessed to determine whether the defects can be rectified. If the issues are minor, the flanges can be sent back to the previous stages such as machining or forging for corrections. However, in the case of serious defects that cannot be repaired, these flanges will be discarded, often melted down for recycling so that the material can be reused in the future production cycles. This ensures that every product that leaves the production line meets the required quality standards and that resources are used efficiently.
Step 5: Painting
The inspected flanges will be sent to the automatic painting production line,where they will be painted in accordance with the customer’s specifications. The painting process not only enhances the appearance of the flange but also provides protection against corrosion and wear.
The paint used is carefully selected based on the material of the flange and its intended application. For example, water-based paints are often used for carbon steel flanges, while epoxy or polyurethane paints are more suitable for stainless steel flanges. The painting process is essential in ensuring the longevity and durability of the flange, especially when it comes to outdoor or corrosive environments.
Our 100-meter Automatic Painting Line
Our production facility is equipped with a state-of-the-art 100-meter automatic painting line designed to ensure the highest quality in flange finishing. The painting process is a careful, step-by-step process that takes approximately 1.5 hours for each batch.
The process begins with washing, where each flange is thoroughly cleaned to remove any dust, oil, or other contaminants that could interfere with the paint application. Washing is crucial to ensure the paint adheres properly to the surface and provides a smooth finish.
Next, the flanges are dried. This step is essential as any residual moisture on the flanges could cause the paint to bubble or peel. Drying ensures a clean, dry surface for the paint to adhere to, enhancing the lifespan and appearance of the flange.
The third step is painting, where the flanges are coated with paint in accordance with the customer’s specifications. Our advanced painting systems ensure an even, flawless coating that enhances both the aesthetic and functional properties of the flanges.
Finally, the painted flanges are dried again. This second drying step is crucial in ensuring the paint is fully cured and hardened, further enhancing its durability and corrosion resistance.
Our 100-meter automatic painting line ensures a meticulously controlled, optimally efficient painting process that guarantees the highest quality finish, contributing to the overall durability and longevity of our flanges.
Step 6: Packaging
The last step in the production process is packaging. The flanges are carefully packed to prevent any damage during transportation. The packaging method varies depending on the size and quantity of the flanges.
In conclusion, the production of a forged flange is a complex process that requires meticulous attention to detail at every stage. Each step, from material selection to packaging, plays a crucial role in ensuring the quality and reliability of the final product. By understanding this process, you can appreciate the effort and expertise that goes into producing each flange.
#JSFITTINGS #RAYOUNG #STEELPIPE #FLANGE #STEELPIPE #MADEINCHINA #MANUFFACTURER #FACTORY #PIPEELBOW #PIPE REDUCER #INDUSTRYFLANGE
Email: admin@jsfittings.com
Whats App: 008618003119682